Devices are becoming smaller and thinner, requiring circuit boards that can fit into the equipment without adding any additional weight while being flexible enough to route around components. Flexible printed circuit boards offer high-density electrical connections while also reducing space.
Paul Tome
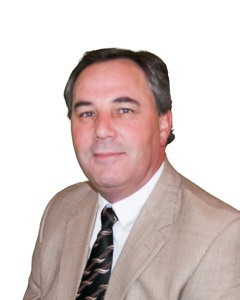
Recent Posts
Rigid-flex circuit boards are the integration of rigid PCB technology with flexible circuit technology in one unit that is capable of both interconnect and operating functions in a device.
There are a wide variety of flexible circuit board design options available to solve interconnect requirements. One of the more unique is a dual access flex PCB construction. This unique construction of a dual access flex circuit can be beneficial for many applications.
The unique capabilities of flexible circuits allow for additional design elements that are not available in rigid PCB designs. A very common one is integrating Pressure Sensitive Adhesives (PSA) into the design. A PSA is a double-sided adhesive tape that can serve multiple purposes. The PSA is attached to the flex as part of the manufacturing process and the release film is retained on the exposed side to protect the adhesive until it is installed.
Identifying the differences between rigid PCB FR4 materials and flex circuit polyimide materials can be useful to customers who are implementing flex circuit designs for the first time. Beyond the obvious difference in flexibility, the two types of materials have different available thicknesses, copper types, and properties that impact high-speed controlled impedance signals.
The hot air solder leveling surface finish (HASL) is the second oldest surface finish available for printed circuit boards and up until a point in time was virtually the standard surface finish used in the electronics industry (originally with leaded solder and more recently the RoHS version with lead-free solder).
Flex circuits have many unique capabilities to solve design challenges. One of these is a lap joint capability that allows a flexible circuit board to be directly attached to another circuit or component eliminating the need for any type of connector.
Contrary to some customers’ perspectives, flex circuits are not indestructible. As with any part that contains a metal if it is bent or handled beyond its physical capabilities it will break. In this blog, we will cover the 3 main causes of fractured or cracked circuits in a flex design and how to prevent them from occurring. We’ll also review how to determine the minimum bend capabilities of a flexible circuit board design.
Heat dissipation is the ability of a part, whether a circuit or any other component, to take the heat that's being generated by a component or an element of the design and to distribute it, dissipate it, and make the heat go away, for lack of a better phrase. This prevents the temperature of the part from continuing to elevate as the device is operated.
Flexibility is a critical element in most flexible circuit board designs. Whether it’s to meet a tight “one-time bend-to-fit” application or a “dynamic” infinite bend cycle application. To meet these requirements, a flex circuit design must be kept as thin as practically possible, use the correct copper type, and utilize the correct copper plating process.