Custom cable assemblies use various types of plugs, connector housings, and gasketing to mate and properly seal within a system. These connectors provide a way to mechanically attach to the other system components by means of a latch or a polarized connector body.
Steven J Goodman
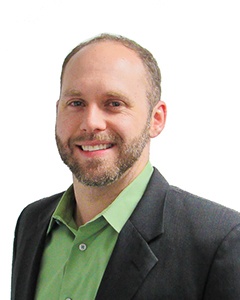
Recent Posts
There are several reasons to choose silicone or PolyTetraFluoroEthylene (PTFE) jacketed cable when designing a custom wire harness. Both jacket constructions are known for their high-temperature resilience and extreme flexibility. The main difficulty of selecting a PTFE is the fact that they can be a bit hard to come by.
Silicone is one of the most common materials used for elastomeric technologies today. Silicone elastomer is utilized across numerous industries and applications, from o-rings to cable jacketing, to cookware, to even your child’s fidget toy, silicone elastomer is chosen for its exceptional mechanical properties and low reactivity.
Touchscreens are everywhere. From the coffee maker in the breakroom to the smartwatch on your child’s wrist to the in-flight entertainment system on your commuter flight, touchscreen technologies are a part of our everyday lives. As touchscreens continue to become intertwined in our culture, they help make everyday tasks that much simpler and improve the ease of use for all kinds of electronics.
Outdoor cables are used in commercial, industrial, and residential applications where they are exposed to a variety of adverse conditions. To survive a lifetime’s worth of abuse, outdoor-rated cables must be designed to stand up to the elements, rough handling, excessive moisture, extreme temperatures, and contaminants like sand or dust. Having an overmold in the design of the cable assembly, the cable terminations can be sealed and ruggedized allowing for several design risks associated with outdoor use to be addressed in an economical fashion.
Our nation’s warfighters demand the highest reliability vehicles, weapons, and communication systems that exist. Lives depend on these products working the first time and every time. They rely on the quality and reliability of the electronics behind their state-of-the-art systems.
Cable assemblies are needed across various industries and are utilized in goods that include consumer electronics, industrial products, mil areo, and even medical devices. Low cost does not mean low quality; in fact, low-cost cables are qualified for use on many high-reliability applications.
Specific to medical devices, handheld electronics, rack-mounted equipment, and other instrumentation utilize membrane switches as a low-cost and high-reliability solution for keypad and button technologies. There are countless button and switch options available for the plethora of design requirements that exist. Medical professionals use these buttons as the primary way to interface and operate the device.
Emerging from the COVID-19 pandemic has been especially challenging for many electronics manufacturers. As the world’s production flood gates opened, deliveries that were on hold for the past year are now being asked to be rushed and pulled ahead.
Shielded cables are ubiquitous across nearly all industries. Not to be confused with armored shielding, which is designed to physically protect a cable, shielded cables are used to safeguard against electromagnetic energy and the negative consequences from signal corruption, blown components, or even a failed qualification test. Cable designers will specify whether a shield is required and its general construction. But just adding a shield to a cable may not be enough to achieve the required performance levels that are anticipated.