One of the most common reasons for selecting a custom cable assembly is to satisfy some type of flexibility or bending requirement. Even the bulkiest of electrical cables have some sort of give to them, allowing them to form around corners or be coiled.
Steven J Goodman
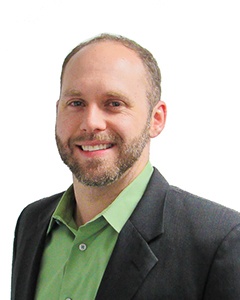
Recent Posts
There are many forms of Night Vision Imaging Systems (NVIS) that help our nation’s warfighters, pilots, and other professionals. Known as Night Vision Goggles (NVG), these devices are highly specialized and amplify various wavelengths of light allowing the user to “see” in darkness.
Cable assemblies used in the medical the industries have to be biocompatible, made of a material that will not cause issues or adverse effects when coming in contact with the body. The material should not cause any type of toxicity (whether it is to the skin or to internal organs, bone, blood, or tissues) that could endanger a person's health.
Overmolded cable assemblies are widely known for their superior performance, attractive cosmetics, and the fact that they can be customized for nearly any application. But overmolded cables also require a sizable investment in hard tooling well before the first cables are ever produced.
When it comes to selecting the appropriate cable type for a multi-conductor , there seems to be an endless combination of wire sizes, jacket materials, conductor arrangements, and shielding methodologies.
When sourcing custom cable assemblies, customers seek the highest quality design and manufacturing capabilities at the lowest costs. Due to these factors, many customers source their custom cable assembly builds from offshore manufacturers. These cable assemblies may consist of ordinary data cables, low voltage wire harnesses, high-resolution video cables, or something completely custom.
Electronic devices requiring custom cable assemblies place our customers into a unique situation. They require a custom cable to ensure that their devices can operate for the desired application, but also require these cables to be manufactured in a timely and economic fashion.
Medical devices are used globally to diagnose health issues and provide life-sustaining care. These devices need to have quality parts and components to operate, including cable assemblies that provide a variety of functions. Due to the nature of these devices and the industry in which they are used, manufacturers must ensure quality management processes are put into place. If a product malfunctions while in use, it could put the patient's health in jeopardy.
When tackling any new project, it’s human nature to focus on the most difficult and uncertain tasks first, while leaving the perceived low-risk and simple activities for the end. When it comes to developing a new product, whether it be for a medical device, commercial widget, or even a mil-aero box build, the initial focus is on the major system elements.
Front panels, bezels, and other types of human to machine interface equipment use several circuit technologies to operate. These circuit types usually involve some form of printed or etched traces using conductive materials like copper and conductive ink. These custom layouts are routed across insulating sheets and films, eventually becoming circuit boards and flex circuits. Dome switches, LEDs, and touchscreens can be added to these everyday circuit boards, bringing them to life as a high-technology HMI solution.