Somewhere around the turn of the century, maybe in the last decade or so, there was a change in the job market. New requirements for employees coming into the job market, a higher standard. The days of getting high paying jobs based simply off prior work experience are behind us; that experience still means something, but not as much as it used to. So what are employers looking for then? A college degree.
Epec Engineered Technologies
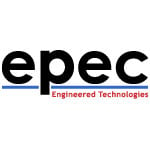
Recent Posts
At Epec, we take workforce training very seriously. We readily invest in workforce education because it is a time-tested, proven path to improving manufacturing process development and customer satisfaction. In our experience, the educated worker is not only productive, they are adaptable problem solvers focused on satisfying our customers' most demanding needs.
The future of manufacturing in the U.S. is set up to be driven by volatile economic conditions, 3D printing, robotics, mobile technology, the Internet of Things, embedded devices, and other emerging technologies. Forecasting the future is always risky, but there are several factors converging right now that bring more clarity as we begin our journey into the second decade of the 21st century.
One of the most critical elements of producing any cable assembly or harness is the amount of cable assemblies testing that is done when the product is completed in manufacturing. There are many methods and levels for testing cable assemblies, but all testing has one goal – to ensure that the product meets or exceeds its specifications.
Packaging for user interface assemblies is the last step in the manufacturing process, but not a step that should be rushed. Epec pays as much attention to packaging detail as we do to design and manufacturing of custom assemblies. Because each assembly part number is customized, each has different size, mass, and shape. However, styles of user interfaces can be grouped into several categories. Experience has shown the type of packaging that works best is based on complexity of construction, shape, size, mass and shipped unit volume. No one packaging solution works for every assembly style.
One point that anyone involved with cable assemblies understands is that "every electronic or mechanical component will eventually reach the end of its life cycle". This blog post will define cable assembly obsolescence as the point in an assembly’s life cycle when it is either no longer in a usable state, meaning it is not functioning as it was designed, or there is no longer a use for the cable assembly due to technology changes.
At Epec, our staff members are our most valuable resource and we believe in empowering employees for success. In this company, we celebrate each others success and support each others challenges. We strive to attract, hire, develop and retain passionate, talented, high performing individuals that are driven by our mission which is to provide a cost savings, technical resource and delivery advantage for our customers. We are committed to recruiting the best people that want to share our success, fit in our culture and live by our core values.
This blog post addresses custom user interface testing in terms of functional test schemes that are completed prior to shipment. Generally, the first user interface assemblies shipment are for First Article acceptance testing where customers fully examine the first units for mechanical and electrical compliance to all engineering drawing and specifications.
When we think of manufacturing in the 21st Century, we picture automated machines rapidly pumping out new products with ease. So why can't the process of complex wire harness manufacturing become fully automated as well? To answer this question, we need a deeper understanding of cable harnesses and how they are prepared.
A cable harness, also referred to as a wire harness, cable assembly, wiring assembly, or wire loom, is a grouping of wires and/or cables that are used to transmit signals as well as provide electrical power if needed. The wires and cables are joined together using a combination of straps, cable ties, cable lacing, tubing (either shrink tubing or non-shrink tubing), sleeving, electrical tape, conduit, and braided extruded string.
Cable pre-molding, sometimes associated with potting or encapsulation, is used to protect the termination points from the surrounding environment. Pre-molding involves the application of a material around the back section of a connector where the termination points are located.