When creating your SMART user interface design, the operating environment should be taken into careful consideration. Environmental contaminants, moisture, temperature extremes, UV radiation, and overall wear and tear from use in outdoor environments are factors that should be considered before determining material and component selection for your SMART user interface.
Epec Engineered Technologies
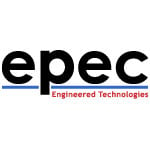
Recent Posts
Before designing your custom human-machine interface project, it's important to have an idea of all the steps involved before and during production. Each step has variable length so while there isn't an exact timeframe for production, having a more informed viewpoint is critical to everyone's ability for following HMI design best practices.
We find that return merchandise authorizations (RMAs) are a powerful statement of a customer’s level of dissatisfaction. RMAs can offer evidence if a manufacturing process fell short of its goal, there was a lack of communication throughout processes, or even misdiagnosed a problem. In any case, we stand behind our product and are ready to support our customer.
When dealing with requests for custom manufactured custom assemblies, the question that frequently comes up is, "why should a jacketed cable be used in an assembly?" The answer to that question can be determined by looking at three key areas: environment, safety, and cosmetics.
Manufacturing cable assemblies used in precision medical device applications requires rigorous demands just to meet the industry standard. When dealing with these specific applications, failure is not an option. Envision applications used in a medical environment. You must limit the possibility of failure for users in the field. Even something as mundane as cable sterilization can potentially cause the cable to fail and/or cause issues for the user(s).
We’ve received custom cable assembly requests on a hand-drawn dinner napkin, 8x11 pieces of paper, and even old photos. Regardless of the format, once the request is received it is drawn into a basic design which is sent to our engineering team. We need to have the requested cable assembly design in a particular format in order to be able to manufacture the request appropriately. Otherwise our facility would not be able to understand dimensions, etc., correctly. An official manufacturing ready design drawing would then be returned to you.
Navigating through the complex cable industry can be both difficult and time consuming. This is especially true if, for whatever reason, you have to change your cable assembly manufacturers. This blog post is intended to give you a perspective of what to expect if you find yourself in the need of switching an existing cable assembly design to a new supplier.
Cable Assemblies can be used in almost any environment, but some environments pose specific challenges that need to be individually addressed. One such environment is when a cable assembly is installed in areas highly susceptible to rodent damage. Installations requiring rodent protection can include any outdoor application, indoor industrial installations, residential applications, food/grain storage areas, or any area that offers shelter and food for rodents.
Business-to-business (B2B) is now more competitive than ever. Remaining competitive in the electronics manufacturing industry requires businesses to change, adapt, and improve. But, there are many barriers to improvement. How does your organization solve problems and drive improvements?
When building a lithium-ion battery pack, there will always be some sort of protection circuitry necessary that will safely separate the cells from the external connections. The protection may be as simple as a pair of charge and discharge Field Effect Transistors (FETs) with voltage and current detectors, or as complicated as adding firmware controlled fuel gauging and secondary protection.