Discrete wire, or lead wire, is the backbone of any interconnect or cable. Within this blog post we break down for you the anatomy of the basic hookup wire and the compositions that can be used as a single unit or grouped together to produce a multi-conductor or multi-pair cable.
Epec Engineered Technologies
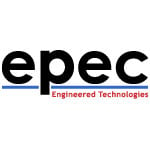
Recent Posts
Heat shrink tubing, also known as heat shrink, is a shrinkable tube that shrinks radially when exposed to heat. Produced using a two-step process, heat shrink is available in a wide range of materials to suit almost any application. Heat shrink tubing has many useful applications, including to provide electrical insulation to wires, connections, joints, terminals, and splices, as well as bundling loose items such as wires and as a protective covering.
Here at Epec Engineered Technologies, we believe that our customers come first. Everything we are is because of our customers. We also strive to make sure that our employees are happy. We are part of a family and we want to make sure we work as a cohesive team; in fact, throughout our facility you will often hear the phrase “One Team, One Fight”.
There are many areas to consider when designing and building cost-effective custom cable assemblies. The areas of primarily importance to be reviewed are the raw material selection, ensuring your assembly is designed for ease of manufacturability, choosing the correct connector, and correctly specifying the criteria the assembly should meet or exceed. If all of these areas are optimized correctly in the design stage, you stand the best chance of keeping your manufacturing costs as low as possible.
Root cause analysis is a technique performed to identify the underlying reasons why a particular problem is occurring. At Epec, we do a lot of problem solving. As manufacturers, we strive to discover better, more efficient ways to delight our customers. Whether we are working on an 8D CAPA or running an A3 Project, we are often working to determine the foundational cause of issues as the means to solving the problem.
As custom manufactured cable assemblies have grown in complexity, it has become far more common to see various electronics integrated directly into the finished design. The inclusion of electronics into a cable assembly design can consist of adding a switch, PCB, LED, or a multitude of other components. Once added, these components offer a much higher level of sophistication to the cable assembly while allowing the included electronics the ability to withstand a much more rugged working environment.
EMI (electromagnetic interference) and RFI (radio-frequency interference) are disturbances generated by external sources that impact a cable assembly by degrading the assembly's performance or completely preventing it from functioning. These disturbances can cause problems ranging from an increase in error rates of the signal being transmitted through the assembly to total loss of any electronically readable signal.
As a full service custom battery pack manufacturer, we prioritize providing our customers with the highest quality battery pack assembly while keeping you under budget. Many of the battery packs manufactured by Epec go into mission critical devices, which require nothing short of the highest quality rugged and reliable batteries. In this post we will look at three key aspects of Epec's US manufacturing that enable us to meet and exceed our goals.
It is important to be aware that certain applications will have battery packs that may be exposed to corrosive elements such as acidic, salt, and on occasion conductive substances and fluids. Over time this type of exposure can slowly corrode the PCBA, components, and solder joints. This type of corrosion can cause premature failure, short circuits, and or dangerous conditions that could lead to fire or even an explosion.
How do you ensure that your manufacturing talent is an asset to your business? Consider a typical manufacturing organization. Qualifications for many entry–level shop floor positions are modest. New hires range from novice all the way to seasoned manufacturing professionals with specialized skills.
Sometimes it is an employer’s market and at other times, there is a scarcity of suitable job talent. In this ever changing environment, how do we keep the most ambitious, hardworking, and engaged workers?