As a premier supplier of human-machine interface (HMI) solutions, our engineers work with and design several types of membrane switches. From tactile and non-tactile response switches to the emerging technology of capacitive touch switches, we have provided proven quality for our customers depending on their needs.
Epec Engineered Technologies
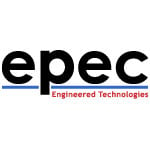
Recent Posts
At Epec, engineers are expected to find innovative solutions to problems and develop them quickly and accurately so that customers can get quality products delivered on time. In this blog post, I will discuss how the 80-20 rule can be used in conjunction with our classic engineering design process to reach solutions faster.
Maybe you have heard of technical writing before, or maybe this is your first-time hearing about it. The chances are good, however, that you have seen or experienced technical writing already in your life. It is an established practice within the industrialized world, but what is it?
At Epec we work on such a varied and technical catalog of products, so our engineers must be comfortable leveraging every manufacturing technology available to them in order to create solutions in design and production. One of the most important technologies that we use is 3D printing.
Working in the manufacturing industry, you’ve probably noticed the letters RoHS or REACH on various documentation or even browsing our website. But, have you ever wondered what these letters stand for or what the certification that comes with them entails?
From controlling condensation on electronics to keeping food warm, flexible heaters provide many advantages to commercial industries such as medical, electronics, aerospace, food and beverage, and refrigeration. Silicone and Kapton® heaters are the most common heaters used due to their flexibility, great thermal transfer, rapid warmup and varying temperature applications.
In my last blog post, I reviewed the 5 why problem-solving method. In this blog post, we will continue this discussion so if you have not seen Part 1, I suggest you read that post first and then come back here.
Manufacturers requiring localized heating for their applications turn to the advantages of flexible heaters that are mounted to components and equipment. These heaters can provide low level or high-level heat at varying temperatures to offer the appropriate thermal transfer based on the applications.
Whether used in the aerospace industry to de-ice equipment, or the food industry to bring ingredients up to a suitable temperature, flexible heaters provide the right amount of generated heat based on the application. These types of heaters can be attached to smooth, bulky and curved equipment in different sizes and functions.
In my last blog post, Five Why Root Cause Analysis Starts with a Good Problem Statement, I recommended that problem-solving teams develop well-crafted problem statements. This blog post will discuss the best practices for the five why method of root cause analysis.