When talking about flexible heaters, determining the amount of efficient heat necessary for the application is required. A range of factors impacts generated electrical heat, including the materials that are used, the wattage, the voltage, the size of the heater, and the pattern of the conducive materials within the heater. One of the vital factors in designing a flexible heater revolves around Ohm's Law.
Epec Engineered Technologies
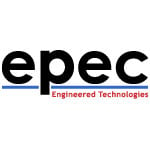
Recent Posts
Polyimide flexible heaters are highly desired in industries such as aerospace, medical, food service, military, and others to provide controlled heat in specified areas in their applications. This heater type may be used in instrument panels inside aircraft to provide moisture-control properties and to prevent the systems from malfunctioning due to extremely cold temperatures at high altitudes. They may also be found in medical diagnostic devices, analytical test equipment, optoelectronic components, and many other applications.
At the conclusion of our webinar, Reducing Risk in Your Custom Cable Assembly - we had several questions submitted to our presenter, Steven J. Goodman, User Interface & Cable Assembly Product Manager at Epec. We have compiled these questions into a readable format on our blog.
It is not often we build an electronic device without any sort of prototyping, but it can happen given the nature of the project and the deadlines being met. If a customer needs a Human-Machine Interface (HMI) to hit the floor in 2 months, the time to develop and build a prototype is strained as both the customer and design engineers will want to test it and provide feedback.
When applications and products require heating options, polyimide and silicone rubber flexible heaters are ideal for a wide range of uses. With optimal heat transfer, they can provide the right temperatures for electronics, instrument panels, sensors, medical devices, and food service products.
At the conclusion of our webinar, Quick Turns PCBs – Why an Experienced Supply Chain Matters - we had several questions submitted to our presenter, Ed McMahon, CEO at Epec. We have compiled these questions into a readable format on our blog.
When we use electronics in commercial settings, one of the major factors that must be taken into consideration is the different temperatures that the circuitry and wiring will experience. Not every electronic device will be used in a stable indoor working environment like an office space.
At the conclusion of our webinar, How PCB Design Choices Affect Overall Cost from Your PCB Fabricator, we had several questions submitted to our presenter, Ed McMahon, CEO at Epec. We have compiled these questions into a readable format on our blog.
After an engineer has finished their circuit design for a printed circuit board (PCB), the next step is to enter the schematic details into a computer-based schematic capture program such as Altium, Eagle, or OrCAD. The finished printed circuit board will provide the physical assembly and interconnection platform for the various electronic components required by the schematic.
Around the world, different industries have applications and equipment where there will be changing temperatures, humidity, or moisture that can impact how a component operates or processes signals. There may also be instances where a product needs to be at a certain temperature so that it may be processed, such as a liquid chemical or food product that has to be at the right temperature, so that it will be fluid enough to be packaged into containers.