There are several reasons for the need to plug printed circuit board (PCB) holes. Some of the most commonly seen reasons include properly tenting or covering the via with solder mask (isolation), to prevent entrapment (solder, chemistry, flux), to prevent solder starvation (wicking of solder in the hole/surface mount technology (SMT) placement directly on via), and for thermal or electrical purposes.
Jeff Forbus
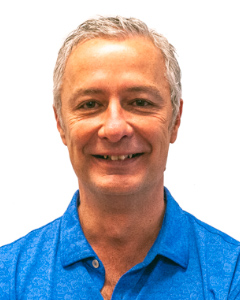
Recent Posts
When it comes to manufacturing printed circuit boards (PCB), providing your PCB supplier with a clean data package can decrease cycle time and ensure requirements are clearly understood.
Printed circuit boards (PCBs) are the heart of electronic products as they provide the conductive pathway for all the electronic components to connect and function together. As electronics become more advanced and complex, PCBs are having multiple layers sandwiched together to establish all the necessary connections.
When manufacturing printed circuit boards (PCBs), the boards will be classified into specific groups based on the level of quality. Any circuit board developed for IPC Class III has met the strictest requirements levels based on tight minimum tolerances and very high precision standards for mission-critical PCBs that can be used in industries such as aerospace, military, and medical applications. Reaching these specific standards ensures that the PCB will endure a long lifecycle, can withstand harsh environments, and will perform at an exceptional level without failure.