Hazardous environments consist of work areas that may experience elevated levels of corrosion, extreme temperature variations, high pressure, flammable substances, or explosive conditions. Devices operating on battery power need special design requirements to prevent the battery pack from becoming damaged due to these hazardous materials.
Anton Beck
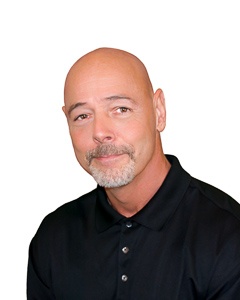
Recent Posts
New technologies, raw materials, and battery manufacturing have paved the way for new trends in custom battery pack designs. Many of these trends focus on making improvements to the battery's capacity and safety, while others redefine the testing standards implemented to ensure battery packs and chargers function optimally for consumers.
Lithium batteries contain high density which is ideal when powering electronics and applications that require a large amount of power over an extended time. However, the battery chemistry is unstable. These batteries can experience overcharging, over-discharging, and discharging that occurs too fast. When the following actions occur, the battery can become damaged, have a diminished lifespan, or even create a safety hazard.
Companies and individuals may store batteries outside the device as backup power when there is a power failure, or when storing extra battery packs. Another reason to store external batteries is when the device won't be used often as the device may drain the battery even when turned off due to internal monitoring systems.
Applications working in indoor and outdoor environments deal with fluctuating temperatures that impact how batteries operate. While batteries have wide operating ranges, working them at the extreme ends of their designated ranges can impact performance and battery life.
Lithium-ion batteries are used for high-powered devices and applications as they provide steady power in demand. They are found in phones, laptops, electric vehicles, and other devices. While lithium-ion batteries provide optimal battery power, optimizing the cell life ensures that the batteries can last for many years.
Due to the vast shapes of electronics and other applications that function on battery power, battery cells also come in different shapes to fit the application. Two common types of shapes are prismatic cells and cylindrical cells. Both offer specific qualities to the application, whether you are looking for cost-effective batteries that are easy to mass produce or batteries with a higher capacity range.
Battery chemistries that are lithium-based must undergo UN38.3 testing requirements before being transported. This testing certifies that the batteries are safe and will not pose a safety risk during shipping over air, water, rail, or road transportation methods.
Around the world, battery pack manufacturers are dealing with supply chain issues. These issues are impacting lead times when they gain battery cell chemistry and battery management system materials.
Charging batteries, whether they are small batteries in laptops to large ones in electric vehicles, requires the right rate of charge based on the battery chemistry. While technology has provided more ways for people to charge their electronics, especially portable devices, customers are looking at ways to speed up the process so they can use their items faster.