As a necessary component in countless applications, custom designed cable assemblies have a major impact on the cost, and therefore the profitability, of any project. Designing a cable assembly that meets both environmental and electrical demands, while keeping costs low, can be a challenging task.
Factors In Cable Assembly Cost Reduction
A key factor for suggesting cost savings on a cable assembly is being able to look at a specification for the entire assembly as well as a detailed BOM listing the components of the assembly.
Having these two documents readily available allows for in-depth analysis of the materials that are included in the assembly and is the starting point for any cost saving suggestions. Additional information will be needed to properly evaluate the assembly though. That information would include the type of environment that the assembly will be installed in as well as the expected service life that the assembly will need to offer.
As mentioned above, there are several factors that can be looked at to try to save costs when designing or reviewing a cable assembly. Those elements are raw materials, expected service life, and manufacturing location.
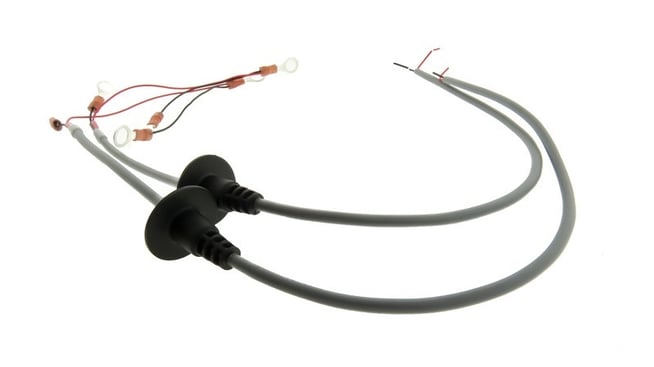
Custom Built Cable Assembly Utilizing Cost Saving Techniques
Raw Materials Used in the Cable Assembly
The raw materials chosen for an assembly will be determined by both the electric performance expected of the assembly and the environment that assembly will be used in. From a simplistic standpoint, there are a limited number of components if a cable assembly – connectors, the medium that will transmit the power or data, and ancillary items such as shrink tubes and labels. The biggest cost savings will come from the choosing of the correct connector and wire/cable to meet the requirements of the assembly.
Cable Assembly Connector Cost Savings
In all instances, the assembly needs to mate with an interface of some sort – which could be another connector mounted to a board, a panel mounted connector, another cable mounted connector, or hard wired to a piece of equipment, to name a few of the possibilities. The type of connector chosen will have an impact on the cost of the assembly. At the low end of the cost would be a connector that can be installed on automated equipment. This type of connection would consist of lugs, terminals, or contacts that are crimped on the wires.
At the other end of the cost spectrum would be connectors that need to be hand soldered onto the wires because of performance needs. These are two ends of the cost spectrum and there are many options that could be explored that lie between these two extremes – again the correct choice will be based on the transmission characteristics that the assembly is expected to handle. Over designing needs to be avoided but an understanding of the type of signal to be sent through the assembly will dictate the connector choices to be explored. In addition, substitution of a connector with equal form/fit/function could provide a costs savings.
Type of Wire Cost Savings
The wire and/or cable that is used in an assembly can be a major cost savings, though the type of wire or cable used will be dictated by the environment the assembly will be used in as well as the signal that will be sent through the assembly. The majority of all assemblies used in North America will require some sort of safety rating. The rating will refer to either a UL or a CSA certification which will be based on the environment the assembly will be used in. For instance if the assembly will be used as an interconnect within a piece of equipment the certification could be in the form of an AWM (Appliance Wiring Material) Style.
If the assembly is to be installed in an air handling area of a public building the certification will need to be in the form of Class 2 or 3 circuit which will carry the designation of "P" after the rating such as CL2P, CL3P, or CMP. The certification needed will determine the compounds that need to be used as both an insulator on the primary wires and as the sheath material. Again, the goal is to not use more costly materials than is needed to meet the safety requirements that the application dictates.
Cable Conductor Size, Material, and Plating
The same philosophy holds true when choosing the conductor size, material, and plating; though the choice will be driven more by service life expected of the assembly as well as the type of signal sent through the assembly. As a rule of thumb, the smaller the AWG size of the conductor, the less expensive it will be – to a certain point. There is a point where the conductor cost will increase as the size of the conductor decreases due to the manufacturing issues associated with the smaller conductor.
The number of strands that make up the overall conductor have an impact on the cost. Again, the rule of thumb is that as the number of individual strands increases the flexibility of a conductor increases but so does the cost. Based on these general rules, a conductor should be as small as possible to allow the transmission of the signal or power and be composed of the smallest number of strands as possible for the application. Choosing the smallest conductor size as the smallest number of strands will allow for the most cost effective solution.
Check out our PowerPoint below:
Summary
Both the point of manufacture for various components as well as the final assembly offer opportunities for cable assembly cost savings. Depending on the complexity of the assembly, labor can take up a significant portion of the costs of an assembly. Choosing the manufacturing location could offer savings, with some non-US settings offering lower labor costs.
The best course of action for obtaining the lowest assembly costs is to work closely with your chosen assembly producer. By working closely and having open discussions, the best possible cost solution can be found by understanding the assembly, where it will be installed, and what performance criteria are used.