Extensive research and development in the battery manufacturing industry has pushed out vast innovations in the custom battery pack segment. The need for these battery packs has grown exponentially due to higher-performance products, utility companies utilizing storage devices, and the expansion of electric and hybrid vehicle markets.
Batteries, such as lithium-ion, are expected to see strong CAGR investments and growth of upwards of 8.2% by 2026. It has created increased competition in the battery manufacturing market.
With this growth, customers are left with assorted options regarding how to customize their batteries for specific applications. It has also led them to tread lightly when they are trying to balance battery pack performance against rising costs. Bringing in a battery pack manufacturer into the preliminary stages of custom battery pack design can create cost savings while still maintaining battery pack performance.
Battery Pack Customization Options
When it comes to battery packs, what you want to be customized can vary. A customer may select an off-the-shelf battery pack yet want a more customized battery management system (BMS). They may also do the opposite by getting a customized battery cell yet selecting a commercial or standard BMS.
Battery pack customization encompasses many factors including the following:
- Cell chemistry
- Connectors & wire assembly
- BMS components
- Charging devices
- Power management integrated circuits (ICs)
- Enclosures & venting
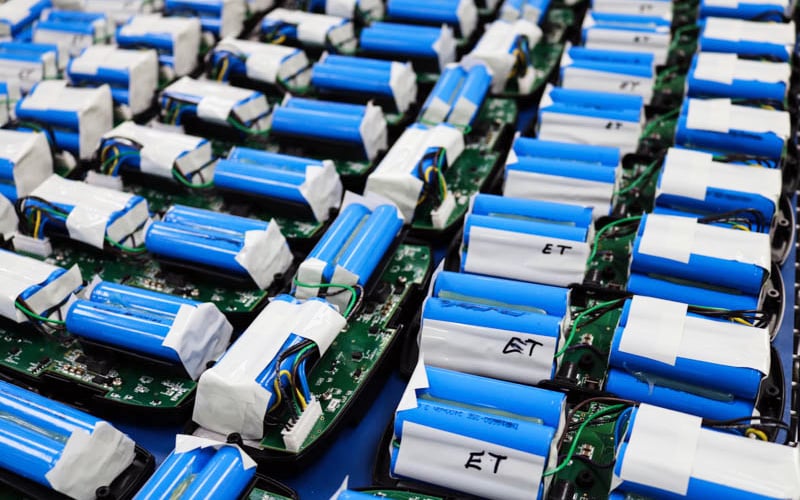
Battery pack customization with various options.
While taking standard or commercial components and using certain customized features can allow some customers to obtain the battery pack at lower prices, there are limitations. An off-the-shelf component or pack will have a set parameter for its capabilities that cannot be changed by the developer. This aspect can lead to customers obtaining battery packs that will not meet the performance needs of their application.
Battery Pack Brand Considerations
Another important cost vs. performance factor for custom battery packs is the brand. There are low-tier to high-tier battery brands. Why certain brands cost more will be based on the cell and chemistry in the pack. When both the cell and chemistry are the same between manufacturing brands, the difference will lie with the electronics.
A basic battery pack brand will have electronics that are pretty standard across the board. They offer charging, discharging, temperature, and short-circuit protection. Costs and quality will begin to increase based on the additional features of the electronics. Such features may include fuel gauging, sleep mode, cell balancing, logbook functions, state of health/charge (SoH and SoC), and many other factors.
Also, take into consideration the application requirements that will play an important factor in a battery pack's cost and performance. Certain industries, such as medical, aerospace, and military, will require specific safety and performance features. These requirements may be set by the specific company, be recognized as national or international industry standards, or be regulated by governmental organizations. Developers will have to abide by these set features for the battery pack, which could increase costs.
Some industries may also require battery packs to receive transportation certification. Transportation certification organizations may request a certain number of samples that will be destroyed during testing. Taking into account these charges can be determining factors in how to design a custom battery pack while managing costs.
Component and Material Factors
Customizations in the components can involve the ICs, connectors, enclosures, and other devices. The types of materials used for these parts can influence costs. For example, you may decide on using aluminum terminals due to their lightweight design for mobile devices. They are also cheaper in price due to being easier to produce. Yet aluminum has less mechanical strength and conductivity as well as is more susceptible to corrosion. Copper and gold-plated connectors offer better conductivity but have more weight and are more expensive.
When considering ICs, the charging profile of the IC and the charging requirements of the application will have to be considered during the design phase. Depending on the type of charge (trickle, constant current, constant voltage, and fast charging) as well as charge determination will impact the types of safety features and other configurations of the ICs.
The charger topology will also be dictated by the battery pack series, cell count, system power management path, input voltage range, and safety features. Evaluating the topology, charging profile, and power management path can dictate the types of ICs to use that is appropriate for the custom battery pack that are economical without sacrificing performance.
Summary
Due to applications having differing requirements, as well as cost differences between battery brands, the best approach to getting the custom battery pack is to perform extensive research. Learn about the application industry, component trends, material market, and manufacturer capabilities to have a better idea of the types of customizations that are available.
Then, reach out to a battery manufacturer like Epec. The manufacturer can inform you about newer technologies and materials that can be used for the design and offer cost-effective alternatives that will give you the best performance without significantly raising your established budget.
Key Takeaways
- Balancing Cost and Performance: Custom battery packs require careful planning to balance rising costs with performance needs, especially in high-demand sectors like medical, aerospace, and electric vehicles.
- Customization Options: Battery pack customization can include cell chemistry, connectors, BMS components, enclosures, and venting. Using off-the-shelf components with custom features may reduce costs but could limit performance.
- Impact of Battery Brand: Battery brand selection significantly affects cost and performance. Higher-tier brands often feature advanced electronics, such as fuel gauging, state of charge (SoC), and state of health (SoH) monitoring.
- Industry-Specific Requirements: Certain industries mandate stringent safety and performance standards, transportation certifications, or regulatory compliance, which can increase costs.
- Material Choices Influence Costs: Materials like aluminum are lightweight and affordable but less conductive and durable than copper or gold-plated connectors, demonstrating the trade-offs in component selection.
- IC and Charging Profile Considerations: The charging profile and charger topology impact IC selection and configuration, ensuring safety and efficiency while optimizing cost.
- Partnering with Manufacturers: Engaging a manufacturer early in the design process provides access to the latest technologies and cost-effective alternatives, helping to optimize performance within budget constraints.